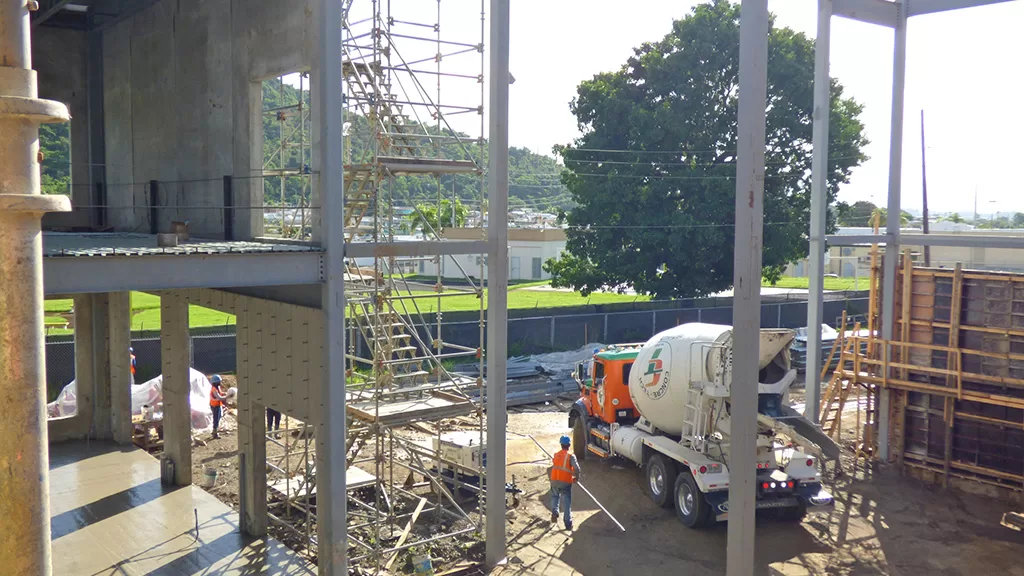
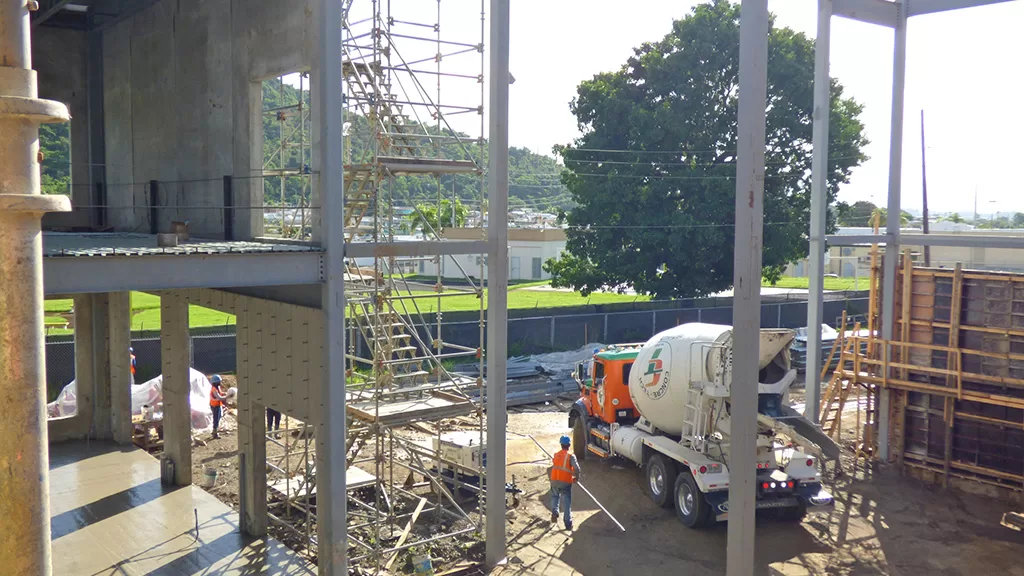
The explosive growth of e-commerce in recent years has forced significant changes in the way warehouses are being designed and built. The Covid-19 pandemic made online shopping more attractive to consumers, further advancing e-commerce and the warehousing business that sustains it.
Warehouses have been around since prehistoric times, when civilizations relied on family- or community-owned pits to store and protect their food supplies. Gradually, warehouse spaces evolved into distribution centers dedicated to shipping and receiving. Today, warehouses are much more than storage space: They are high-tech logistical hubs designed to optimize supply chains in an extremely fast business environment.
They are also bigger, taller and stronger than they were 20 years ago. Architects and builders must keep up with the ongoing transformation of the warehouse sector, where success starts with the proper utilization of space. The right space can improve the flow of shipping and receiving, boost productivity and avoid unnecessary costs.
Here are five trends that show where the modern warehouse is heading now and in the near future.
The growth of e-commerce over the past few years has created a need for massive warehouses to store and move extensive inventories. While warehouses in urban areas tend to be smaller because of a lack of space, bigger warehouses are sprouting in suburban and rural areas.
According to Statista, existing space size of industrial big-box property in the United States from 2013 to 1st half 2023. The existing space of big-box distribution buildings in the United States has grown steadily in the past 10 years. In 2023, the big-box building inventory amounted to approximately 2.9 trillion square feet. Big-box buildings refers to large industrial buildings used for distribution. In 2023, there were over 6,000 big-box buildings in the U.S.
Warehouse 1 explain that currently in the United States, the average warehouse size is a little over 15,000 square feet. Small warehouses are thus considered to be under 15,000 sq. ft. and large warehouses are those over 100,000 sq. ft.
Warehouses are not only expanding horizontally; they’re getting taller. Modern warehouses are being designed and built or remodeled with 40-foot clear heights instead of the typical 20 feet. Raising the ceiling is a cost-effective way to create much-needed square footage in urban areas.
With consumers expecting greater product availability and faster shipping times, more e-commerce retailers, especially in densely populated areas, are choosing to increase their storage capacity by expanding their warehouses vertically. Keeping distribution centers physically closer to their customers allows retailers to fulfill last-minute purchases and cut shipping times, giving them a critical competitive edge. As a result, more companies are favoring multi-level warehouses in or near urban centers over spread-out, one-level facilities.
Developing large warehouses near major population centers is not always an option because of lack of suitable land and the higher costs involved. Consequently, more warehouse companies are opting for remodeling existing spaces rather than building from the ground up. Converting an old mall, for example, into a warehouse, means the project already has the land, structure, utility access and other resources in place.
They can choose to utilize the standard warehouse dimensions that work best for their business’ needs.
These days green is everywhere, and the warehouse sector is no exception. More sustainable and energy-efficient systems and practices are being incorporated in the design, construction and operation of warehouses, storage and distribution centers.
Now, and especially in the future, when the Gen Z generation takes over the economy (and the world), businesses must stay up to date with climate change issues that are important to consumers and audiences throughout the world. Their goodwill should not be underestimated.
Green Systems and Practices Trending in the Warehouse Sector
Proper ventilation and air filtration have always been elements of warehouse design, but in a historically tight labor market in which workers can be more selective about their employers, comfort is no longer a luxury.
While different warehouses have needs that are unique to them, it is important to consider these and other factors that can play an important role in the health and well-being of employees.
The pandemic taught us many lessons, among them that people and companies should be ready for potential eventualities and have back-up plans in place before they need them.
With this new awareness, warehouse and distribution centers, which are crucial to the local and global flow of products, are taking steps to be as adaptable, flexible and efficient as possible, thus changing the way these facilities are built.
For more information about warehouse design and construction or if you’re ready to discuss your project, give us a call or send us a note. We have the expertise and passion for construction needed to ensure a successful warehouse project.