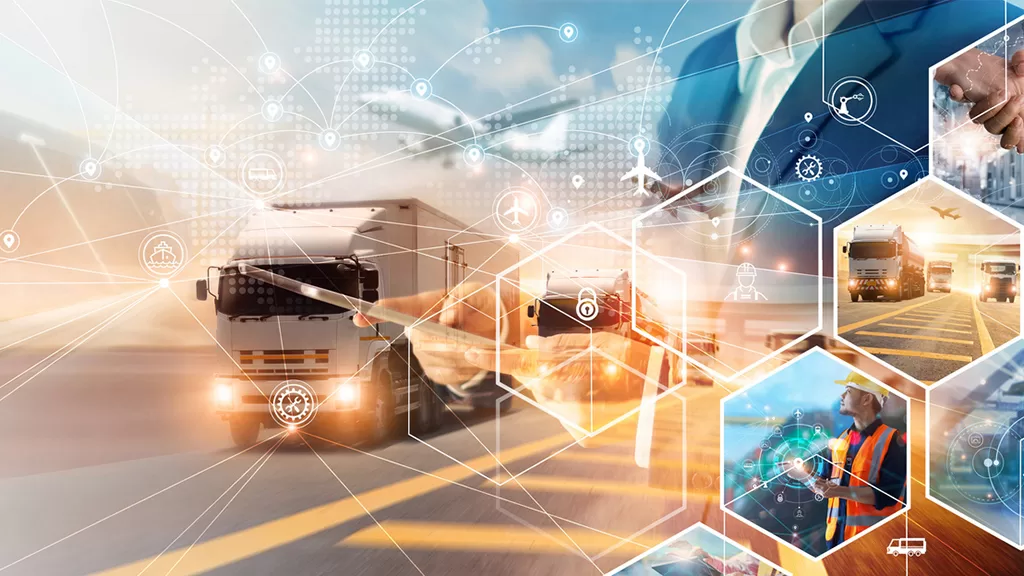
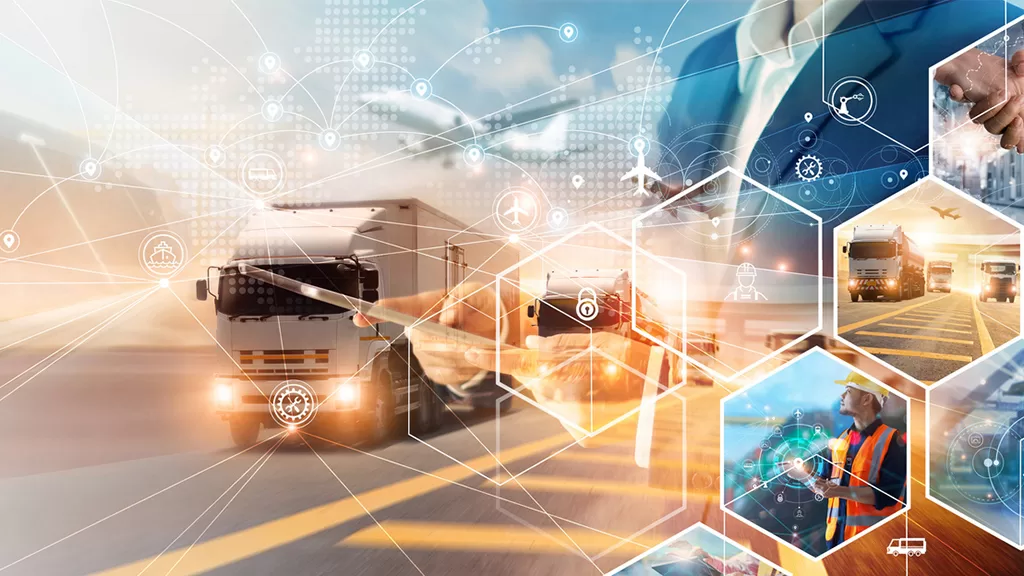
Supplier management plays a vital role in the construction industry, where the timely delivery of materials, equipment and services is essential for the successful completion of projects. Managing suppliers goes beyond simply selecting vendors; it involves meticulous planning, coordination and monitoring to ensure that all elements align with the project’s timeline, budget and quality standards.
Every phase of a construction project depends on reliable suppliers, from the initial groundbreaking to the final touches. In an industry that often deals with unpredictable variables–weather, labor shortages and fluctuating material costs–effective supplier management can be the key to mitigating risks, controlling costs, and maintaining project efficiency.
Supplier management in the construction industry refers to the systematic approach to sourcing, coordinating and overseeing suppliers who provide essential materials, equipment and services. The process involves everything from identifying the right suppliers, negotiating contracts and managing deliveries, to ensuring that all materials meet the required standards of quality and safety.
Construction projects typically rely on a diverse supply chain, including multiple categories of suppliers, each responsible for delivering specific materials or services. Given the complexity of modern construction projects, supplier management is crucial to avoid delays, cost overruns or substandard materials that can lead to long-term issues.
The goal of supplier management is to create a streamlined supply chain that ensures consistent delivery of the right products at the right time, allowing construction teams to stay on schedule and within budget.
The construction industry typically works with a wide range of suppliers, each specializing in different materials or services essential to a project. Understanding the different types of suppliers helps in developing effective management strategies tailored to their unique roles.
Material suppliers provide the essential raw materials for construction, such as concrete, steel, lumber, bricks, glass and more. These materials form the backbone of any project, and their timely delivery is critical to keeping construction moving forward. A delay in raw materials can halt entire phases of a project, leading to significant cost increases and missed deadlines.
Equipment suppliers are responsible for delivering or leasing the heavy machinery and tools required for the project. Cranes, bulldozers, excavators and other specialized equipment are often needed at specific times, and poor coordination with equipment suppliers can cause bottlenecks on-site.
Read also: Construction Estimating in Flash: 6 Key Principles of Accurate Project Costing
Construction projects often rely on external service providers for tasks such as plumbing, electrical work, HVAC installations, etc. These subcontractors or service providers need to be managed effectively to ensure their work integrates smoothly with the overall project.
Certain construction projects may require highly specialized materials, such as environmentally sustainable products, high-tech finishes or unique architectural elements. These suppliers often work on custom orders, requiring additional lead time and quality assurance processes.
To manage suppliers effectively, construction companies must establish clear strategies that account for everything from procurement to post-delivery performance. Below are the key elements of a successful supplier management system.
The first step in supplier management is choosing the right partners. This involves a rigorous process of pre-qualification, where potential suppliers are evaluated based on their financial stability, track record, product quality and ability to meet delivery schedules. Construction companies often issue Requests for Proposal (RFPs) or Requests for Quotation (RFQs) to gather detailed information from suppliers.
Once suppliers are selected, negotiating contracts is a critical phase. Clear terms regarding pricing, delivery schedules, quality standards and penalties for non-compliance should be agreed upon. Contracts must also account for contingencies, such as delays or fluctuating material costs, to protect the project from potential disruptions.
Effective communication between construction teams and suppliers is essential to maintaining a seamless workflow. Regular updates on project timelines, changes in material needs and any issues that arise must be communicated clearly. Establishing a point of contact or using digital project management tools can streamline this process.
Read also: Top Soft Skills That Lead to Success in the Construction Industry
After a supplier has been onboarded, it’s important to continuously monitor their performance. This includes tracking delivery times, material quality and adherence to agreed-upon specifications. Any delays or deviations should be addressed promptly to avoid further disruption to the project.
Supplier risks can arise from multiple factors, including financial instability, production issues or logistical problems. Developing a risk management plan involves identifying potential risks in the supply chain and creating contingency plans to address these challenges. This might include maintaining a list of backup suppliers or securing long-term contracts that lock in pricing and availability.
Rather than treating supplier relationships as transactional, it’s beneficial for construction companies to cultivate long-term partnerships. Building trust with reliable suppliers leads to better pricing, priority service, and improved flexibility when dealing with urgent or unexpected project needs. Suppliers who understand the construction company’s goals and processes are more likely to deliver consistent results.
Using technology to manage suppliers can significantly improve efficiency and transparency. Construction management software that includes supplier portals, real-time tracking of deliveries and performance analytics can streamline the entire supply chain process. This technology allows project managers to make data-driven decisions, reducing the likelihood of errors or delays.
Supplier management is a cornerstone of successful construction project execution. By effectively managing suppliers, construction companies can avoid delays, control costs and ensure that quality standards are met. As the construction industry continues to advance with new technologies and sustainability goals, supplier management will remain a critical area for improvement and innovation.
With years of experience in managing diverse supplier networks, CIC Construction Group has the knowledge and skill to make sure that your materials, equipment and services are delivered on time and to the highest quality standards. Contact us to learn more about how we can assist with your supplier management needs and keep your project running smoothly from start to finish.