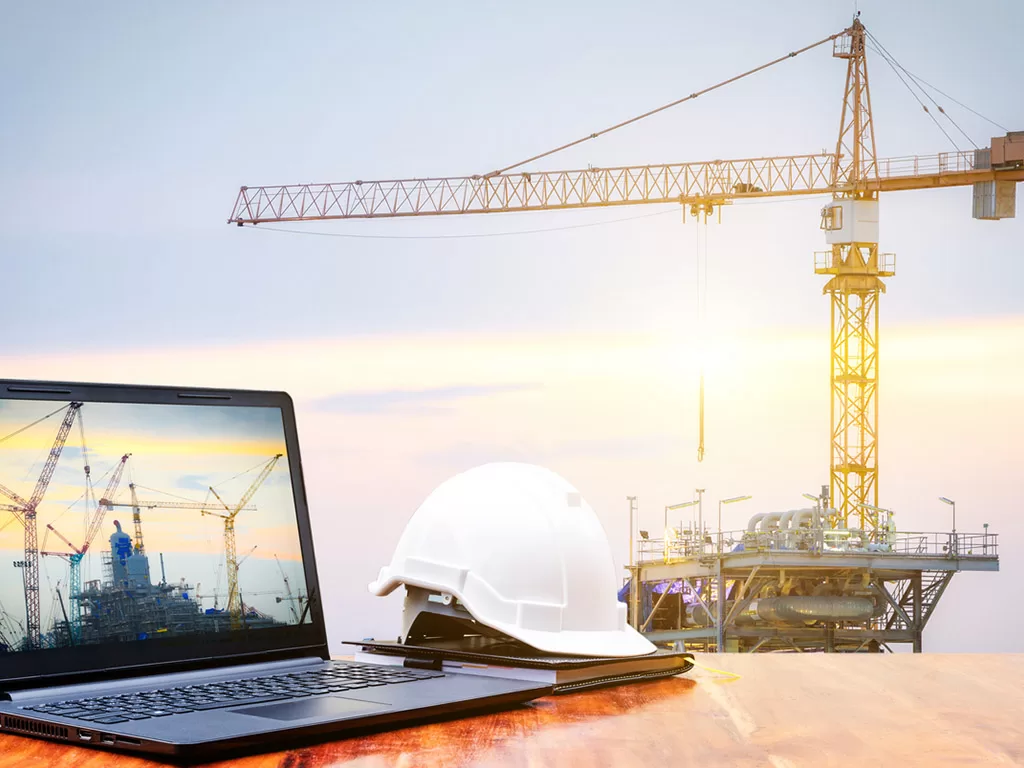
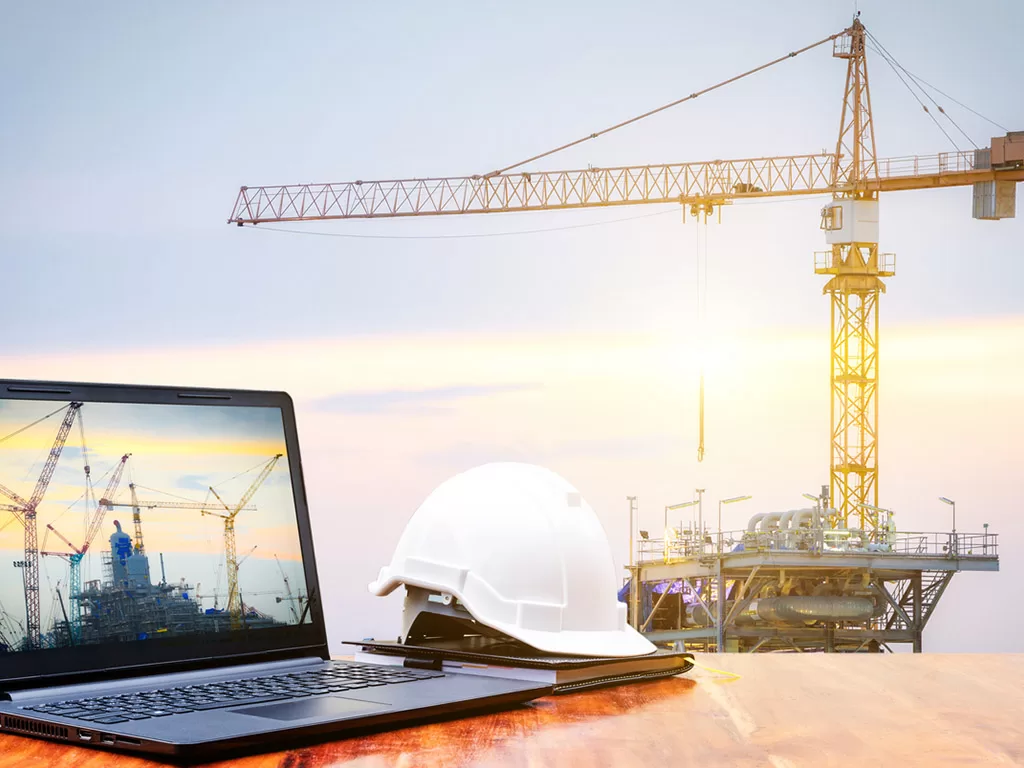
Like other industries, the construction industry is undergoing a digital transformation, driven by cutting-edge advancements such as digital twin technology. Digital twins are changing the way buildings are designed, constructed and maintained, leading to more efficient, sustainable and cost-effective projects.
Digital twins are virtual replicas of physical assets, processes and systems that can be used to simulate, predict and optimize their performance. These virtual representations are created by gathering data from the physical asset. The data is then used to create digital models that precisely mirror the physical asset.
Digital twins are dynamic, updating in real-time or near real-time to reflect changes in the physical counterpart. By integrating data from various sources, including sensors, drones and software systems, digital twins provide a comprehensive, 360-degree view of a project at any stage of its lifecycle.
The technology can be used to simulate the behavior of the physical asset under different conditions. Architects, engineers and builders use it to test design ideas, predict performance and identify potential problems.
Unlike building information modeling (BIM) diagrams, which show its many systems and subsystems, digital twins show space. Where BIM focuses on how the building’s constructed, digital twins focus on how people will use the space.
READ ALSO: What Is BIM and How It Has Revolutionized Construction
As a powerful tool for planning, visualization, analysis and management, digital twin technology can be used in all phases of the construction process, from design and planning to construction and operation.
In the design phase, digital twins are used to create virtual prototypes of buildings and infrastructure, allowing architects and engineers to test different design ideas and visualize the finished product before construction begins. During construction, they enable real-time monitoring, which aids in managing resources, tracking progress, identifying potential problems and coordinating activities between different subcontractors, thus improving efficiency and reducing costs.
In the post-construction or operation phase, they offer valuable insights for facility management, maintenance and future renovations. Digital twins can be used to monitor the condition of buildings and infrastructure and optimize performance, helping to extend the lifespan of assets and reduce maintenance costs.
Different types of digital twins are used in construction, depending on the specific application.
They’re also commonly divided into these categories:
Level 1: Descriptive Twin
The descriptive twin is a visual replica with live, editable design and construction data, including 3D models and BIM.
Level 2: Informative Twin
The informative twin uses increased integration with sensors and operations data for insights at any given time.
Level 3: Predictive Twin
The predictive twin captures real-time data, contextual data, and analytics to identify potential issues.
Level 4: Comprehensive Twin
The comprehensive twin leverages advanced modeling and simulation for potential future scenarios as well as prescriptive analytics and recommendations.
Level 5: Autonomous Twin
The autonomous twin has the ability to learn and make decisions through artificial intelligence, while using advanced algorithms for simulation and 3D visualization.
As mentioned earlier, there are many benefits to using digital twins in construction. Here are the top eight:
Digital twins offer a detailed visualization of the project, enabling better decision-making in the design phase. This leads to fewer errors and changes during construction. For example, using a digital twin to simulate sunlight exposure throughout the day can influence the design of window placements and energy-efficient lighting systems.
With real-time data and analytics, construction processes in all phases become more efficient, reducing delays and cost overruns.
Digital twins can help to reduce costs by identifying potential problems early on and by optimizing performance.
The technology can help to improve the quality of construction by allowing architects and engineers to test design ideas and by helping to coordinate activities between different subcontractors.
Digital twins provide a central platform for all stakeholders to access and share information, improving coordination and communication.
Post-construction, digital twin technology can predict when parts of a building may need maintenance, reducing downtime and repair costs.
Because it allows for more accurate planning and resource management, digital twin technology contributes to more sustainable construction practices.
By simulating the impact of different scenarios, digital twins can identify potential safety hazards, leading to proactive measures to prevent accidents.
Despite their benefits, integrating digital twins into construction processes is not without challenges:
Digital twin technology marks a new era in construction, offering new advantages in efficiency, sustainability and project management. While challenges exist, the benefits they bring to the construction industry are undeniable. As this technology continues to evolve, it will undoubtedly become an integral part of the construction landscape.
Contact us to learn more about how digital twin technology can benefit your construction project.