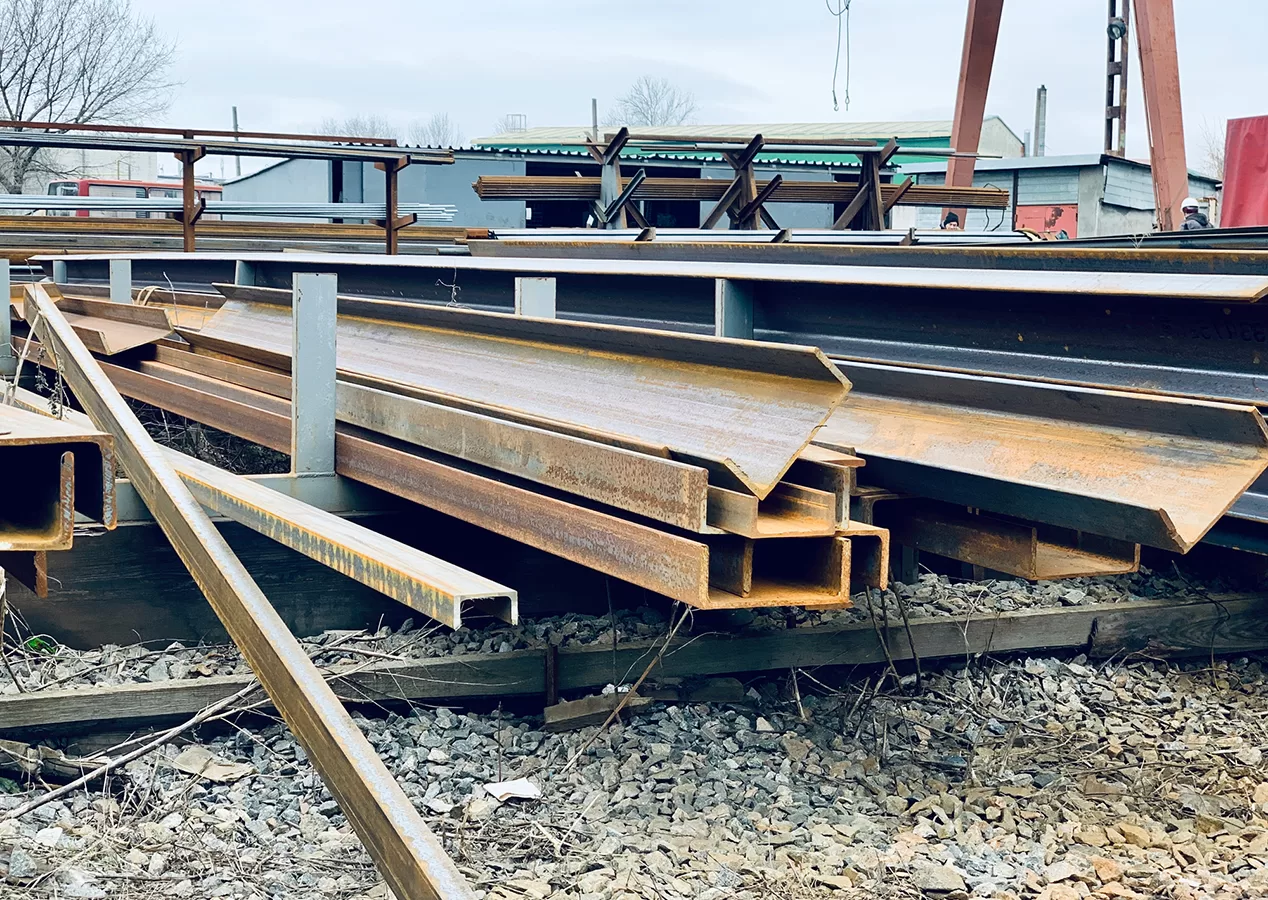
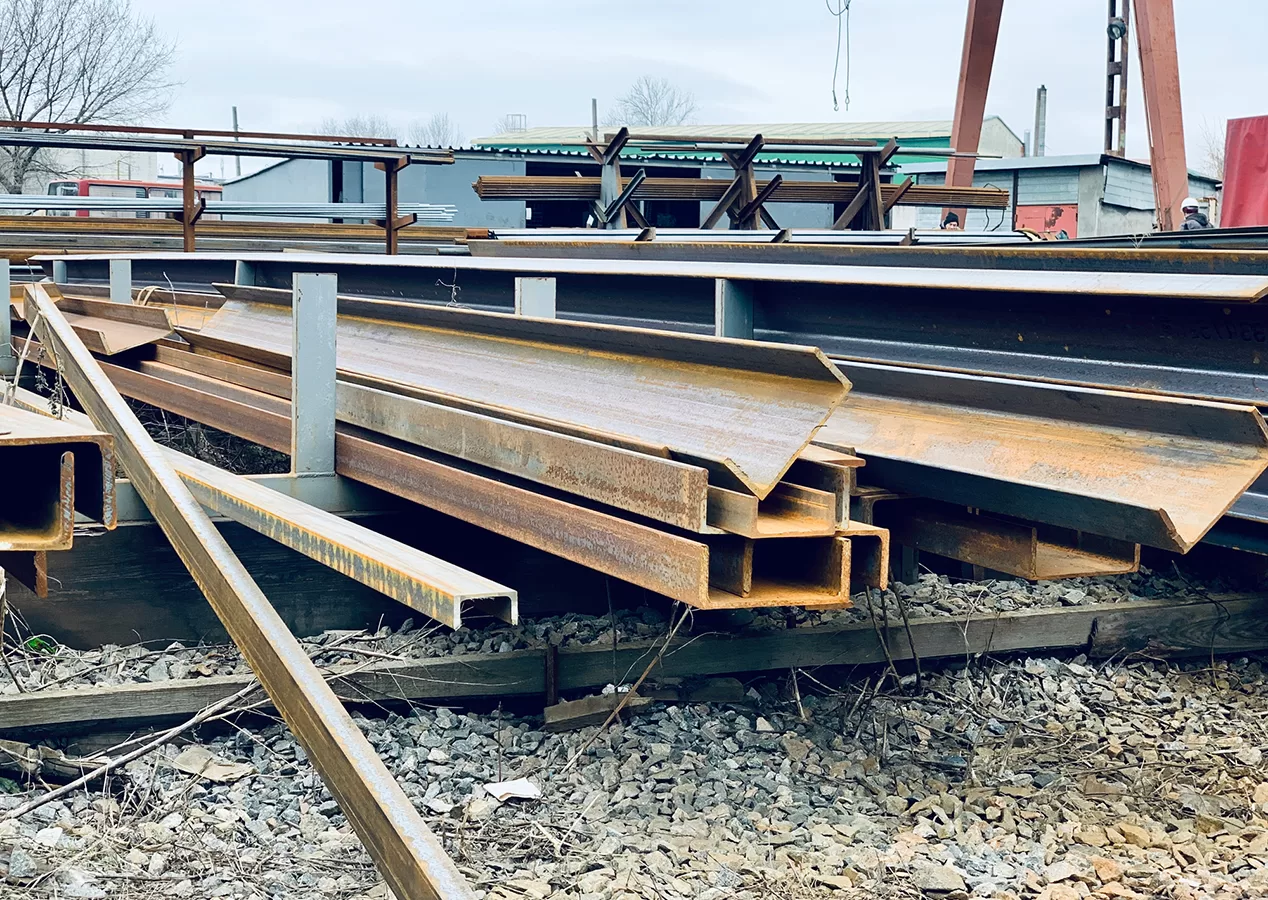
San Juan, Puerto Rico – March 9, 2022.
The Covid-19 pandemic has wreaked havoc on global supply chains, significantly disrupting every sector of the economy. In the construction industry, a lack of building materials and equipment has increased costs and caused delays, forcing builders to change how they do business.
The early signs of supply chain constraints were double-digit price hikes for two key construction materials: steel and lumber. Availability of these and other materials dropped thanks to labor shortages stemming from factory lockdowns and workplace restrictions. Border closures, transportation issues, logistical bottlenecks, political instability, adverse weather, and natural disasters further affected supply chains, leading to cost overruns and project delays.
“Prices have gone up across the board, directly affecting project schedules and budgets,” said Carlos Hermida, Procurement Manager at CIC Group “Many construction materials are either not available or taking four times longer than usual to be delivered.”
While supply chains are out of their control, contractors can take steps to mitigate risks and fight the supply chain woes. Here are the top nine.
Under current conditions, the time it takes to acquire construction materials can stretch from weeks to months. Therefore, it’s imperative to order supplies in advance to allow additional time for delivery and avoid having to overpay and delay projects. The client can make early payment to the contractor, who can provide security (such as a bank guarantee) for an amount equal to the early payment. Extending the arrangement beyond traditional long-lead items may help ensure that materials are received within the required time and at predictable prices.
Stocking up is not as simple as just hoarding product. While demand exceeds supply, the price of key construction materials goes up, but prices could settle in the near future. Furthermore, some materials have shelf lives that need to be considered. Building stocks for immediate delivery or to have the materials on-site is ideal, so contractors need to find a balance between stocking up and avoiding potential pitfalls.
When dealing with materials that are difficult to obtain or that are prone to unpredictable price fluctuations, builders and clients should consider alternate or substitute materials. Comparable brands or different types of materials may be suitable for a project. However, there are circumstances in which strict safety or performance standards call for specific products to be used; using different products invalidates performance or quality testing. Brand loyalty could present obstacles, as customers often have brand preferences they’re unwilling to change.
Right now it makes sense for builders to cultivate relationships with multiple construction materials and equipment suppliers in their areas of service. Suppliers understand the turmoil that supply chain disruptions are causing and the need for contractors to establish relationships with various suppliers. When your preferred supplier is struggling to deliver certain materials, there may be one or two others who have the materials you need when you need them.
Contractors typically manage supply chain risks, but in these uncertain times that risk may be shared between builder and client. For example, the contract could include an extension of time right for the contractor without cost. The right would apply when supply chain delays are affecting all contractors working on similar projects and/or apply only to specific materials or locations.
Supply chain disruptions are likely to have an effect on budgets and schedules. Production interruptions lead to product shortages which lead to higher prices and delays. Cost figures from a previous project or year are useless for a project happening when supply chains are in chaos. Contractors encountering supply chain issues should redo or update their cost estimates, both for themselves and for their clients.
While fixed-price contracts are attractive to clients (and their banks), in an environment where the cost of building materials is uncertain, contractors often adjust prices to protect themselves against future price rises. The client could agree to allowing specific materials to be subject to a certain degree of rise and fall so that the client avoids paying too much of a premium for a fixed-price contract.
When scheduling a construction project, it’s not uncommon to add a buffer for unexpected events. However, unforeseen supply chain disruptions might call for increasing this buffer or changing the project’s schedule. When jobs that used to take a week now take a month and deadlines are at stake, contractors should talk to their clients about extending the timeline.
There is no going back to “normal.” For almost two years, since early 2020, construction companies have had to adapt to overcome obstacles brought on by the pandemic. Having learned from their experiences, they’re bound to use a more strategic approach going forward. They will consider potential supply shortages in the future and factor price fluctuations into their quotes. Some will consider price acceleration and force majeure clauses in their contracts. After all, chances they will face similar conditions in the future, whether caused by a natural disaster, political unrest, international trade disputes or another pandemic.